Horstman Steel Nytro Clutch |
The Steel Nytro clutch is the state of the art in kart racing clutches. Newcomers to karting or racers on a tight budget should consider the Yamaha Sportsman Class or the Horstman HPV Spec Class as initial expense and yearly maintenance costs will be substantially lower than other two cycle classes. The clutch makes no power, it only transmits available torque from the engine to the rear axle. In karting the clutch is subject to extreme abuse as it is repeatedly required to perform with a controlled slip which of course creates high heat. The biggest enemy of the clutch as well as your engine is heat. Often a clutch is "smoked" (overheated) for one or more of the following reasons.
1. Stall speed adjustment above peak torque of engine (also called over slipping the clutch)
2. Low oil level or improper oil
3. Lack of maintenance (glazed friction discs, worn levers, etc.)
4. Bad driving skills (cause slower exit speed off corner which builds heat in clutch and engine)
5. Binding of chassis or wrong chassis setup (also greatly affect exit speed)
6. Carburation too lean (wrong adjustment or maintenance)
7. Exhaust flex too short (hurts bottom end performance)
8. Gear ratio wrong
9. Bad fuel
10. Engine timing wrong
11. Chain too tight or not oiled correctly
The Steel Nytro Clutch is to be used only for organized kart racing. For play or other areas of recreation consult with your Authorized Horstman Dealer for the proper clutch.
APPLICATION
TWO DISC Junior & Senior Sportsman classes with can muffler. Junior Piston Port with .600" restrictor and expansion chamber.
THREE DISC Piston Port Light classes with expansion chamber exhaust
FOUR DISC Piston Port Heavy class with expansion chamber
SPECIAL TOOLS REQUIRED
1. One 1 1/8" deep socket (available at most auto parts stores)
2. Clutch Spanner Wrench
3. Clutch Puller
4. Valve Lapping Compound (available at most auto parts stores)
5. 5/16" Allen Wrench ("L" handle or socket style)
6. 9/64" Allen Wrench ("T" handle or "L" handle)
7. 5/32" Allen Wrench ("T" handle or "L" handle)
8. Torque Wrench
LAPPING CRANK TAPER
Before installing the Clutch it is wise to lap the tapered portion of the crankshaft and the tapered portion of the Clutch Hub. Lapping will produce a more precise fit. Place a small amount of coarse lapping compound onto the taper of the crank. Slide the Drive Hub assembly of the Clutch onto the crank and rotate it by hand until the two surfaces are 100% seated. Then wipe off the lapping compound with a clean rag.
INSTALLATION
1. Install Spacer (Item No. 1) onto crankshaft. Be sure the radius side of the spacer faces toward the engine. (See Fig. 1)
2. Apply a light coat of oil to the crankshaft.
3. Slide the Drum onto the crankshaft.
4. Insert the Woodruff Key.
5. Slide the Drive Hub assembly onto the crankshaft. Be sure the keyway in the Hub is aligned with the Woodruff Key. Rotate the Friction Discs to allow the outer lugs to fall into the channels of the Drum.
6. Install the Starter Nut (Item No. 14). Tighten to 350 inch pounds. NOTE: The Horstman Spanner Wrench is helpful in holding the clutch when tightening the Starter Nut.
7. Check end play. (See Fig. 2)
8. Check spring height. (See Fig. 5)
9. Insert Gasket (Item No. 20) into the Oil Cover (Item No. 19)
10. Slide the Oil Cover onto the Clutch with all holes aligned.
11. Insert the six Cover Bolts (Item No. 16) through the Cover and thread into drum. Tighten evenly to insure proper seating and to avoid binding. Spin Clutch by hand to make sure there is no binding.
12. Rotate the Clutch so that one of the Oil Fill Plugs (Item No. 15) is in the 12 o'clock position. Remove that Oil Fill Plug and add oil to just under 2 full. Replace the Plug when finished.
END PLAY
When the Clutch is tightened securely to the shaft you should be able to spin the Drum freely. If the Drum does not spin freely, remove the Clutch and replace the Spacer with a new Spacer of appropriate width available from your Authorized Horstman Dealer. A temporary solution would be to grind some material off of the original Spacer. The recommended minimum clearance is .005" and the maximum is .015". (See Fig 2) If you have over .015" clearance the Clutch may not be properly seated all the way onto the shaft, or you may be using the wrong sized Spacer.
STARTING ENGINE & ENTERING TRACK
The Clutch is designed to permit easy starting with a battery operated Gun Starter. The Gun Starter should have a 5/16" hex drive. When starting the engine be sure to keep the brake engaged in order to prevent any sudden acceleration.
STALL SPEED
Proper stall speed adjustment will enable your motor to operate within its most efficient power band, which should provide the fastest lap time. A tachometer is needed to help you set the stall speed range for optimum performance. Optimum setting should be 200 - 400 RPM below peak torque. The chart below is only a basic guideline. Consult your motor builder or the manufacturer of the exhaust system for precise settings.
CLUTCH MODEL CLASS SPRING P/N STALL SPEED
2 Disc Rookie Sportsman 514200 7400-8000
2 Disc Junior Sportsman 328200 8500-9000
2 Disc Junior .600 Restrictor 328200 9000-9500
2 Disc Senior Sportsman 328200 8500-9000
2 Disc Senior Super Sportsman 328200 9200-9600
3 Disc Yamaha Light 313000 9800-10,700
4 Disc Yamaha Heavy 313000 9800-10,700
4 Disc Piston Port 313000 10,500-10,800
CLUTCH ADJUSTMENT
The basic engagement speed of the clutch is predetermined by Levers that pivot in response to centrifugal force. The pivoting of the Levers is restrained by the six Compression Springs. A variety of stall speeds can be obtained simply by adjusting the spring tension or changing spring combinations.
FOR HIGHER STALL SPEEDS
Increase the preload on the six Compression Springs by turning the Spring Retainers clockwise.
1. Use caution as the clutch may be hot.
2. Turn Clutch until one Oil Fill Plug is positioned above oil level. Remove this plug. (Item No. 15)
3. Insert a 5/16" allen wrench into the Starter Nut (Item No. 14) and rotate engine until a Spring Adjuster (Item No. 17) is visible. This is the proper position for adjusting the Clutch.
4. Insert a 9/64" allen wrench into the adjuster and turn it clockwise 1/8 of a turn (See Fig. 3).
5. Rotate the engine 60 degrees to access the second Spring Adjuster. Insert the 9/64" allen wrench and turn it clockwise 1/8 of a turn.
6. Repeat steps 5 and 6 until all six springs are adjusted as equal as possible.
7. Check the oil level and add oil if needed.
8. Replace the Oil Fill Plug.
NOTE: 1/8 turn of adjustment clockwise should raise the stall speed about 100 RPM's.
FOR LOWER STALL SPEEDS
Decrease the preload of the Compression Springs by turning the Spring Adjusters counter-clockwise while following steps 1. thru 8. Re-enter the race track and determine if you now have the desired stall speed. If not, return to the pits and repeat steps 1. thru 8. If adjustment exceeds maximum limit, you must use weaker springs.
ADJUSTMENT LIMITS
The clutch is designed to work within adjustment limits. Do not exceed the limits or damage to clutch will occur. (See Fig. 4)
Maximum: .340"
Minimum: .285"
NOTE: All Steel Nytro Clutches are preset at the factory at .325". This setting is appropriate for your first stall speed test.
AIR GAP
Air gap is adjustable on all models. A selection of Floaters (Item No. 6) is available from .040" thick to .060" thick in increments of .005". The factory air gap is .050" with normal tolerance of +/- .005". Air gap can be adjusted to suit your engine and pipe setup as well as racing conditions.
Factory preset air gap should be fine for most conditions.
When air density is low...increase air gap by .005".
When track is hot with a lot of rubber laid down...increase the air gap by .005".
For torque setup...decrease the air gap by .005".
Do not exceed the limits per Fig. 5
HELPFUL TIPS
1. Use only Horstman Steel Nytro Clutch Oil as it is a special high temperature lubricant designed to be compatible with the Friction Discs as well as transfer heat.
2. Never check stall speed by engaging the brake while revving the motor. This puts excessive stress on the clutch components.
3. Soak replacement Friction Discs in the Steel Nytro Oil for at least 5 minutes before using the clutch. This allows the friction material enough time to absorb the oil.
4. When racing in wet conditions lower the stall speed 300 to 500 RPM's to help prevent overheating. Reason: Exit speeds are slower which causes the clutch to work harder.
5. Drain oil and replace after each track session (racing or practice). Reason: Lubricant breaks down from heat ... remember clutch contains less than 2 ounces of lubricant.
CLUTCH REMOVAL
1. Drain Oil.
2. Remove Oil Cover.
3. Remove Starter Nut.
NOTE: Spanner Wrench is helpful in holding the Clutch.
4. Thread optional Clutch Puller into Drive Hub and tighten until Drive comes off Crank.
5. Remove Woodruff Key.
6. Remove Drum.
7. Remove Spacer.
DISASSEMBLING CLUTCH
1. Remove Jam Nut (Item No. 12) use 1 1/8" deep socket. This Nut is Left Hand Threaded. Turn clockwise to remove.
2. Remove Coned Washer (Item No. 11).
3. Remove Lever Support (Item No. 8).
4. Remove Friction Discs and Floaters.
5. Remove Springs from Lever Support. Pressure Plate, Levers and Dowel Pins can now be removed.
MAINTENANCE AND REPAIR
The Steel Nytro Clutch is subject to extreme heat and wear due to the high slip conditions. The Clutch must be properly maintained for optimum performance. Remove Clutch and inspect all components after each racing event.
1. Spacer - Item 1
Look for cracks or excessive wear. Replace if necessary.
2. Sprocket/Drum Assembly - Item 2
Oiling the chain before each track session will increase the life of the sprocket. Replace when teeth are worn to a sharp point. Chain adjustment should have at least 12mm of free play. An over tight chain or chipped chain causes immediate sprocket wear. After each race, inspect and re-tighten (if necessary) the eight cap screws that attach the sprocket to the drum. (1/8" allen wrench is required)
3. Friction Disc - Item 5
Replace after 3 - 5 race events in Sportsman Class or 1 - 2 race event(s) in Piston Port / Reed Valve Classes. Reason: Discs do all of the work and are subject to surface temperatures as high as 600 F which causes harmful glazing and oxidation.
4. Floater - Item 6
Check for warpage or a polished surface. Replace as needed.
5. Pressure Plate - Item 7
The pressure plate is precision ground on the surface that engages the Friction Disc. This surface should be checked periodically for warpage or a glazed condition. Replace or regrind if necessary.
6. Drive Hub - Item 4
Check for wear in the triangular area that comes in contact with the Floaters. Check for cracks in keyway or spokes. Replace as soon as cracks appear.
7. Levers - Item 10
The pivot hole in the Lever is subject to extreme stress due to frictional loading from centrifugal force. This causes the pivot hole to eventually elongate. Inspect the Levers for pivot hole wear or cracks whenever you rebuild the Clutch. Replace after 10 races or when worn or cracked.
8. Dowel Pins - Item 9
Replace after five races.
9. Lever Support - Item 8
Check for cracks, warpage, or wear. Replace when any of these conditions appear.
10. Oil Cover - Item 19
Check for cracks or warpage which could cause leaks. Replace if necessary.
11. Springs - Item 18
Replace after 3 - 5 races in Sportsman Class or 1 - 2 race(s) in Piston Port / Reed Valve Classes.
12. Spring Adjuster - Item 17
Replace after 3 - 5 races in Sportsman Class or 1 - 2 race(s) in Piston Port / Reed Valve Classes.
13. Starter Nut - Item 14
Replace when internal hex is worn or when nut is cracked.
14. Oil
Drain and replace after each track session.
ASSEMBLING CLUTCH
1. Clean parts with disc brake cleaner. Disc brake cleaner comes in an aerosol spray can and is available at most automotive parts stores. Do not use gasoline!
2. Install dowel pin into each lever and then into each slot of the lever support.
3. Insert Pressure Plate into Drive Hub.
4. Place each Spring over a corresponding pressure plate stud. Screw a Spring Adjuster clockwise on each stud, but do no tighten yet.
5. Install the proper number of Discs and Floaters.
6. Place the Lever Support assembly over Drive Hub making sure you align the triangular drive lug with the recessed portion of the Lever Support.
7. Install the Coned Washer.
8. Install the Jam Nut and torque to 550 inch pounds.
Note: The Jam Nut is left hand threaded.
9. Now adjust the Spring Retainers to .325".
10. The Clutch is now ready to be installed onto the crankshaft. See the INSTALLATION section of this manual.
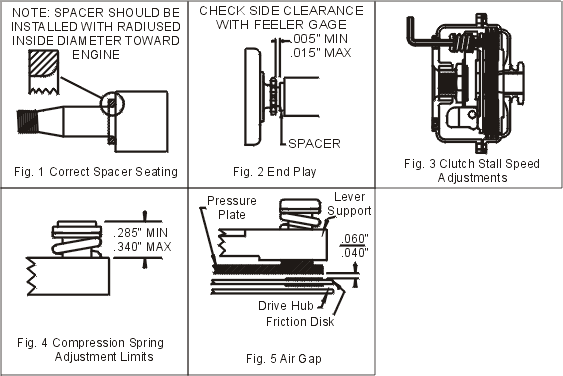
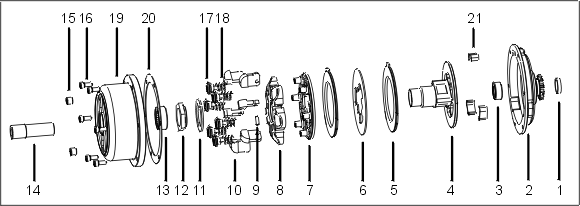