Horstman's newest 4 cycle racing clutch named Greased Lightning. Nothing is faster than greased lightning@. It was developed from our popular MDC series clutch which has been the top clutch in karting for many years. Designed for experienced racers that like to customize their clutch setup to best suit engine and track conditions.
This clutch is made for ultra high performance and requires expert setup and a serious commitment to maintenance.
Warning !!!
1. Clutch and chain operate at high speed.
2. A clutch guard must be installed to provide a protective barrier.
3. The clutch guard should cover the full width of the clutch for best safety. (Figure 1)
Warning !!!
When starting engine be sure the driver has the brake engaged to prevent sudden acceleration. Always check stall speed on the racetrack, not in the pits or on a kart stand as this is not accurate and dangerous because of excessive stresses induced.
Optional Horstman clutch guard for Briggs & Stratton engine available
THEORY OF OPERATION
The Greased Lightning clutch operates by centrifugal force to transmit the engine's power to the axle. The clutch engagement speed can be adjusted for maximum performance.
INSTALLATION
Clutches can be mounted inboard (sprocket facing engine) or outboard. Mounting outboard requires an optional spacer kit.
The crankshaft pto (power take off) of the engine is 3/4" diameter non tapered. The clutch is designed to have a slip fit installation over the crankshaft. A slip fit mounting must never be forced on, otherwise removal may be very difficult. If the clutch will not slide easily onto the crankshaft it is necessary to polish burrs or nicks from the crankshaft or the inside of the clutch hub. A strip of fine grit Emery cloth should be used for deburring. Be careful as the keyway in the pto and the clutch have sharp edges. Always use eye protection and hand protection around sharp objects.
1. Slide clutch onto crankshaft.
2. Align keyway in clutch with the keyway in the crankshaft and insert special clutch key.
Note: Do not force key into the assembly.... a slight amount of filing to the key may be necessary in order to allow a slip fit.
3. Install the flat washer, lock washer, and bolt onto the end of the crankshaft.
4. Torque bolt firmly to 150 inch pounds.
STALL SPEED
Stall speed is the RPM that the clutch hooks up solid. In kart racing stall speed is commonly called clutch slip. If someone asks "Where do I slip my clutch?" they want to know proper stall speed for their setup. Adjusting the clutch for more slip is actually raising the stall speed. Therefore adjusting the clutch for less slip is in fact lowering the stall speed. The best stall speed is the RPM that your motor reaches peak torque. If the clutch engages below peak torque, performance will be sluggish. Consequently if the clutch engages above peak torque power will be wasted in the form of heat in the clutch. Of course excess heat in the clutch should be avoided whenever possible as clutch performance will suffer and damage will occur.
STALL SPEED GUIDELINES
The stall speed recommendations (Figure 2) are for reference only. Finite adjustments must be made to adapt to track conditions, air density, engine setup, etc. From the factory, the clutch is designed for a smooth and positive lockup. However if you prefer a harder lockup, install all weight on levers and replace the black springs with optional red springs.
STALL SPEED ADJUSTMENT TIPS
1. Attach weight per chart (Figure 2).
2. Go onto the track and run 5 laps in order to seat the friction discs. During break-in you should be observing the stall speed to determine how much clutch adjustment is needed. After break-in return to your pit space and evaluate the changes if any which may be necessary.
3. Keep the spring adjustment within limits (Figure 3).
4. Optional stronger or lighter springs are available if adjustment limits have been exceeded.
5. Never install excessive weight (over 4 washers) because additional force on the clutch could cause warpage or premature failure.
TO RAISE STALL SPEED
Remove weight from levers or with an allen wrench adjust all adjustment screws clockwise equally. 1/4 turn of adjustment will raise the stall speed about 50 rpm. Now go back onto the track and have someone check your performance with a stopwatch. Keep experimenting with stall speed adjustments until you have reached your fastest lap time. Now leave the stall speed alone and start testing gear selection and other performance variables.
TO LOWER STALL SPEED
Use the same procedure as above except turn the adjusting screws counter-clockwise or add more weight to the levers.
ADJUSTMENT LIMITS
There are limits on the amount of spring adjusting that can be done before damage to the clutch occurs. (Figure 3) Do not adjust the springs below .250" or they will coil bind (bottom out) before the clutch can hook up solid. This will cause the clutch to build heat from over slipping and eventually burn up. If the limit of .250" has been reached and you still want a higher stall speed, you need to install optional stiffer springs or remove weight from levers. Be careful not to exceed the maximum adjustment limit of .300" as the adjustment screws could work loose. (Figure 3)
INTERNAL CLEARANCE (AIR GAP)
Air gap is the distance of the space between the friction discs and the pressure plate. Correct air gap is important to enable the levers to pivot the prescribed amount for smooth yet firm engagement. Increasing the air gap causes the clutch to engage more aggressively. This does not necessarily improve performance. (Figure 4)
Greased Lightning clutches are preset at .035" air gap ± .010". During operation the friction discs will wear therefore it is important to check the air gap with a feeler gauge about every two races. When the maximum clearance of .055" has been reached due to wear it is necessary to install new friction discs or a thicker floater disc to return the gap to within tolerance. A minimum air gap of .025" is the other end of the tolerance. Anything under .025" gap will cause a lazy performing clutch.
CLEANING
Clean the clutch after every dirt race and every asphalt race. A dirty clutch will overheat and the plates will not slide freely on the splined drive hub which hurts performance.
Remove clutch from engine when cleaning. The best cleaner is any automotive disc brake cleaner. Do not use solvents, gasoline, or soap and water to clean the clutch disks. Wear safety glasses and rubber gloves to protect eyes and hands when maintaining your clutch. It is not necessary to disassemble the clutch when cleaning.
MAINTENANCE AND REPAIR
The clutch is subject to extreme heat and abuse due to the high slip racing conditions. The clutch must be properly maintained for optimum performance. After cleaning inspect the following.
Note: For inspection, the only item that must be removed is the basket. Just remove the snap ring and outer thrust washer. If the friction disks are worn below .110" thick then the clutch should be disassembled and rebuilt.
1. Sprocket / Basket Assembly
Oiling the chain before each track session will increase the life of the sprocket. Replace sprocket when teeth are worn to a sharp point. Chain adjustment should have at least 2" of free play. An over tight chain or chipped chain causes immediate sprocket wear. Check basket for wear and cracks, replace if pins are worn or missing or basket has any cracks in surface. When notched, file aluminum down to the pin to prevent lining hang up. (Figure 5)
2. Friction Disk
The friction disk has a tough steel core with special friction material bonded to the surface. Replace when friction material is glazed or worn below .115" thick or when lugs are worn past .595" wide.
3. Floater
Check for warpage or a polished surface. Replace as needed. You can get extra life by deglazing with medium emery paper.
4. Pressure Plate
A true pressure plate is critical for optimum performance and heat dissipation. The pressure plate is precision ground on the surface that engages the friction disk. This surface should be checked periodically for warpage or a glazed condition. Replace or regrind if necessary. Also, check studs for cracks or loosening. Regrind minimum is .106".
5. Drive Hub
Check for wear in the splined area that comes in contact with the floater. Check for cracks in keyway. Replace if cracked. Any burrs or nicks should be removed for better performance.
6. Levers
The pivot hole in the Lever is subject to stress due to frictional loading from centrifugal force. This causes the pivot hole to eventually elongate. Inspect the Levers for pivot hole wear whenever you rebuild the clutch. Replace when severely elongated.
7. Dowel Pins
Dowel pins are subjected to severe stress and wear. Replace after every 10 races. Apply a light coat of grease or anti-seize to the new pins.
8. Lever Support
Check for wear in slots by the levers. Check for cracks and replace if any cracks are evident.
9. Lever Support Bolts
These bolts are high quality alloy cap screws which are subject to high loads. Make sure they are properly torque and recheck for loosening after each race. If these bolts are removed for any reason they must be replaced. Do not reuse.
10. Springs
Inspect for cracks or broken springs. Also if free length is below .475" replace because the spring is fatigued.
11. Thrust Bearing / Washers
The thrust bearing and washers will last many hours if cleaned frequently and coated with grease.
CLUTCH DISASSEMBLY
1. Remove Snap Ring (Item 1).
2. Remove Outer Thrust Washer (Item 2).
3. Slide Basket (Item 3) off Hub (Item 7).
4. Remove Inner Thrust Washers & Bearing (Item 6A & 6B).
5. Remove Springs (Item 15).
6. Remove the eight Socket Head Cap Screws (Item 18).
7. Remove Lever Support Hub (Item 14).
8. Remove Levers & Dowel Pins (Item 11 & 12).
9. Remove Friction Disks (Item 8) and Floater (Item 9).
CLUTCH ASSEMBLY
1. Set Drive Hub (Item 7)on a flat surface with spline side up.
2. Install a Friction Disk (Item 8), the Floater Disk (Item 9) and a second Friction Disk onto the Drive Hub.
3. Install six Levers (Item 11) and six Dowel Pins (Item 12) into Lever Support (Item 14).
4. Slide Pressure Plate (Item 10) onto Lever Support.
5. Now slide the Lever Support onto the Drive Hub with bolt holes aligned.
6. Install eight new Cap Screws (Item 18) into hub. Tighten to 75 inch pounds.
7. Install Springs (Item 15).
8. Install Retainers (Item 16) onto Springs.
9. Install Adjusting Screws (Item 17).
10. Set spring adjustment at .300". (Figure 3)
11. Turn Drive Hub over with spline side down.
12. Install a Thrust Washer (Item 6a), the Thrust Bearing (Item 6b) and a Thrust Washer over the shaft of the Drive Hub. Remember to apply grease to the washers and bearing.
13. Slide Basket / Sprocket (Item 4) over the shaft of the Drive Hub. Don't forget to apply grease to the bearing.
Note: Align the external lugs of the Friction Disks with the channels in the basket.
14. Install Outer Thrust Washer (Item 2).
15. Install Snap Ring (Item 1).
16. Hold clutch and rotate Basket / Sprocket assembly to check for binding. If basket does not spin freely, check end play. End play can be measured with a feeler gauge placed between the snap ring and the outer thrust washer.
Minimum end play .005". Maximum end play .020".

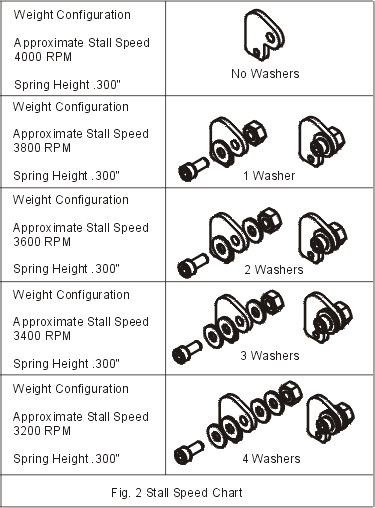
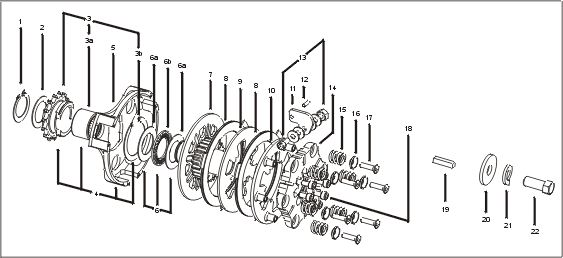
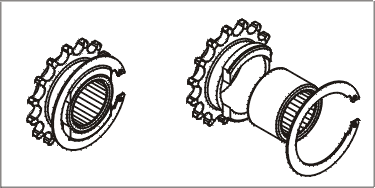
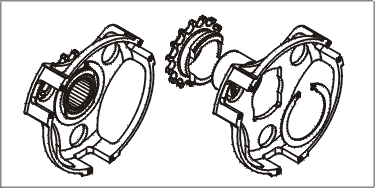